Q&A with Virginia Cosgriff – Operational Excellence Lead – McGough
Operational Excellence Lead Virginia Cosgriff recently earned her Shingo Examiner certification after spending nearly a decade dedicated to earning the distinguished designation. The team sat down with her to discuss her path to earning the rare title and what it means for McGough’s OE moving forward.
How did you first get started learning about Lean?
I recall my first foray into Lean started on the opposite end of the spectrum. I was in a high school pre-engineering course creating a Rube Goldberg Contest machine.
(For the unfamiliar, Rube Goldberg Contests typically involve college or high school students who create a mechanism to complete a simple task. The object – to make a simple task as complicated as humanly possible through reactionary mechanisms set off by a series of events or kinetically moving parts.)
The project drove me crazy, but in a good way. It made me want to really attack learning how to take the seemingly complicated and make it as simple as possible.
How did that impact the start of your career in engineering?
Since that course I’ve dedicated my life to learning and understanding how to build Lean process into organizations. I first got my undergraduate degree in industrial engineering as well as my master’s thereafter, where my thesis was dedicated to Lean. From there, Lean has taken me all over the world, from Japan to South America, working to understand how Lean process across industries function, and how I can apply that learning to my own work.
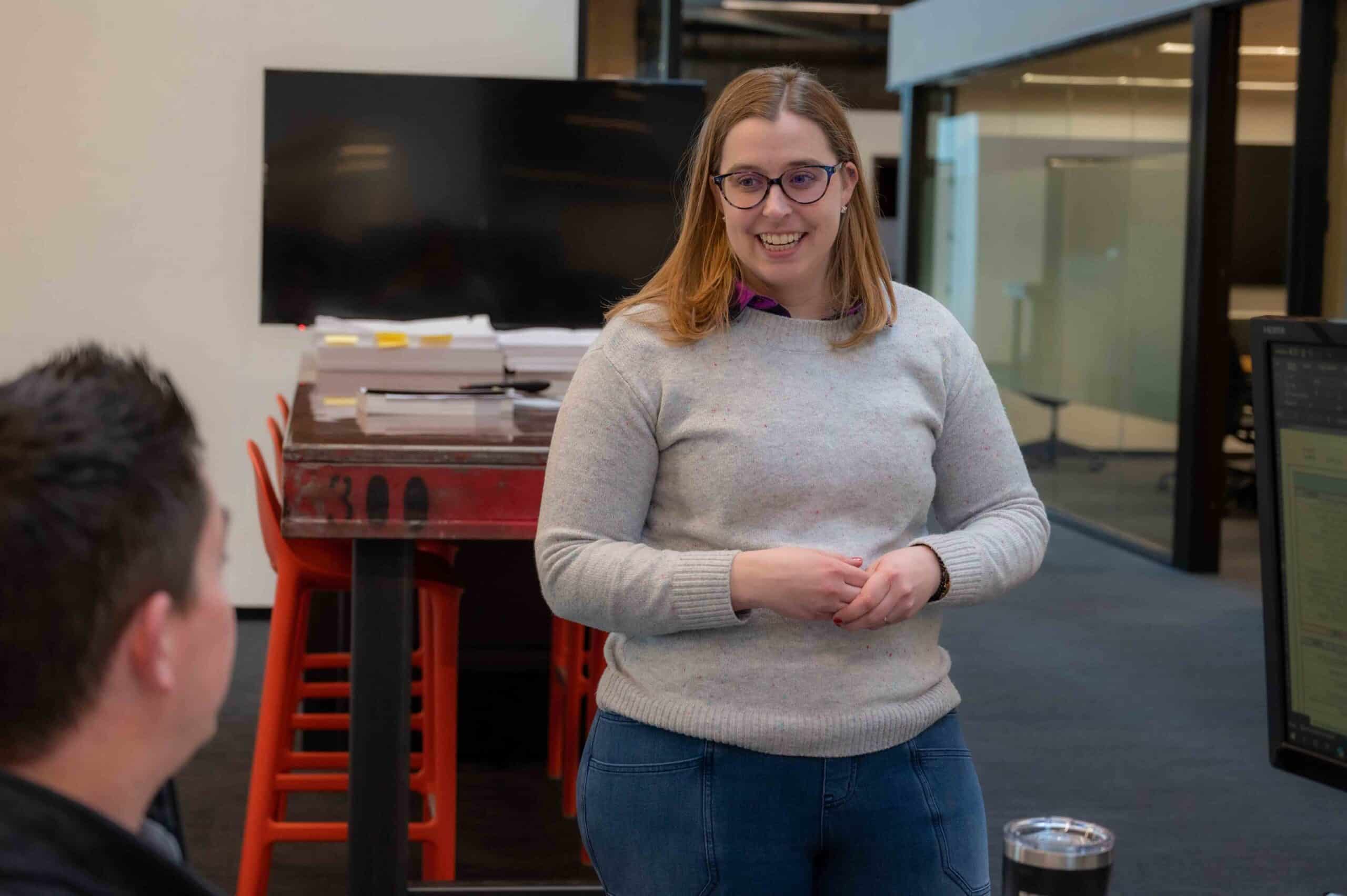
How did what you learn lead you to where you are today?
I initially started my career in healthcare, working for the world-renowned Mayo Clinic helping them implement their first Lean cultural transformation, along with other healthcare systems after that. Since then, I’ve spent the last several years helping McGough adopt a continuous improvement mindset that helps how we do what we do better and more efficiently.
And when did you start your progression with the Shingo Institute becoming an Official Examiner for the Shingo Prize?
The Shingo Institute, founded in conjunction with Utah State University, is built on helping drive organizational and operational excellence through higher learning. As part of the Institute’s core principles includes recognizing and rewarding organizations for pioneering and/or adopting core Lean processes.
To be recognized for a Shingo Prize, organizations must meet certain criteria as part of the challenge. They are then assessed on these criteria by a Shingo Examiner team, which is where the designation comes into play.
I began my process with Shingo during my time at Mayo, nearly a decade ago. The initial process includes quite a bit – you need several sponsors, of which one has to be a current examiner, as well as others working in Lean currently. Applicants must also have somewhere between 8-10 years of applied experience in Lean as well as other criteria outlined by the Shingo Institute.
After beginning the program way back in 2013, I’ve had some of the most incredible experiences getting exclusive access to some of the world’s most innovative companies to understand not only how to implement Lean, but how to use it to affect culture and behavioral shifts.
How’s the program affected you personally and professionally?
It changed my life! My life’s passion was lived out through the process of learning, understanding, and studying peer organizations. It gives me incredible vigor and excitement in my current role moving forward.
What was your biggest takeaway in becoming a Shingo Examiner?
Changing or influencing behavior is really how Lean changes our culture. You can’t just apply tools and hope it works out. If you can understand how our behaviors are negatively impacting a process and why, even if they were following a standard, it typically leads us to a better solution through that learning.
And what does that mean for McGough and Lean in construction?
For McGough, that means a truly advanced understanding of improved Lean process for our own internal programs, but for our customers’ bottom line. I’m one of only ~150 examiners worldwide, so this is a true differentiator for the organization moving forward.
To my knowledge, there’s nobody else in the world who’s a dedicated Shingo Examiner that also works in construction. We have the opportunity moving forward to continue to pioneer Lean in construction and that only means increased savings for both us and our customers.
How does that impact the work we do today?
Through improved Lean implementation, bringing added efficiency to large-scale projects is a must and we’re super excited to bring my experience to this platform moving forward.
Not only does this experience help us implement changes to improve the organization to better serve customers, but it allows us to sustain results and help employees have a better experience working here. The mantra I like to live by is ‘improving every way, everyday’.
If we can make McGough an innovator in our work, I think that’s only going to make working here that much more fun, but less stressful, which is good for everybody.